1. Introduction
In water diversion, flood control and drainage, sewage treatment, farmland irrigation, environmental protection, etc., low-lift, large-flow pump-gate water conservancy projects are widely used. Usually, most of the low-speed pumps used in such water conservancy projects are low-speed pumps below 500r/min. Commonly used water pump motors include asynchronous motors, synchronous motors, and special submersible motors. However, many of the low speeds are achieved by relying on high-speed motors connected to reducers. Since the reducers themselves have mechanical losses and are easy to wear, this type of low-speed pump system also results in low efficiency, high power consumption, high noise and vibration, large volume, and high maintenance.
However, permanent magnet synchronous motors have unparalleled application advantages in such water conservancy engineering applications. The permanent magnet synchronous motor is designed to have a low speed and can directly drive the impeller, eliminating the need for a reducer structure. The overall system efficiency is high, the noise and vibration are small, and the operation is safer and more reliable. It cooperates with the permanent magnet special control system to form a drive system, relying on the huge advantages of energy conservation and environmental protection, and has become a new trend in the development of low-speed pumps.
2. Current application status of low-head, high-flow, low-speed pumps in water conservancy projects
2.1 Shaft cross-flow pump with asynchronous motor + reducer
The structural form and engineering application of the shaft cross-flow pump with asynchronous motor + reducer are shown in Figure 1. This type of vertical shaft cross-flow pump is generally driven by a 4-pole to 8-pole asynchronous motor + reducer. The axial length is large, the reducer gear is easy to wear, and the lubricating oil needs to be replaced regularly. The maintenance workload is large, the maintenance cost is high, and the system is less efficient. Because there are high-speed rotation and friction parts, the vibration noise is high and the system efficiency is low.

2.2 Asynchronous motor direct-driven inclined shaft pump
The structural form and engineering application of an asynchronous motor direct-driven oblique-axis pump is shown in Figure 2. The asynchronous motor speed used in this type of asynchronous motor direct-driven oblique shaft pump is generally between 200 and 300r/min. Although the low-speed asynchronous motor directly drives the reducer, the low-speed multi-pole asynchronous motor is affected by the structure, technology, and heat dissipation. Affected by many factors, the motor structure is complex, the process is difficult, and the motor is large in size, mass, low efficiency, and the power factor cos is extremely small (generally around 0.6, even lower at low loads, and high-power reactive power compensation needs to be configured). Moreover, the reactive current of the motor is large, so the capacity of power transmission and distribution must be increased by at least 1/3.
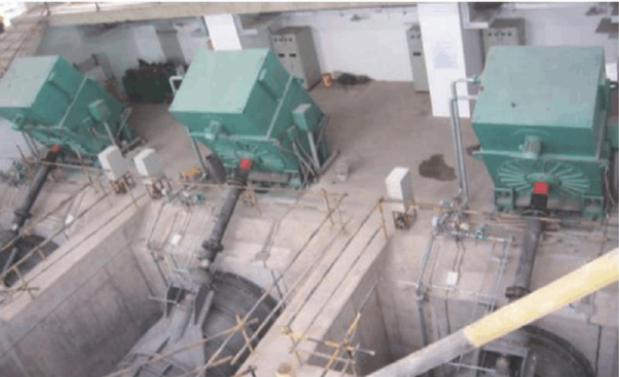
2.3 Vertical low-speed asynchronous motor-driven vertical axial flow pump
The structural form and engineering application of the vertical low-speed asynchronous motor-driven vertical axial flow pump are shown in Figure 3. This type of vertical axial flow pump driven by a vertical low-speed asynchronous motor is the same as the inclined axis pump directly driven by the asynchronous motor. The low-speed multi-pole motor has a complex structure, difficult process, large size, large mass, low efficiency, and extremely low power factor.
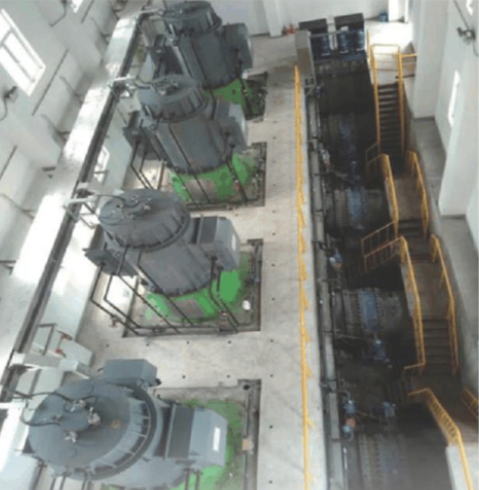
2.4 Asynchronous motor + reducer and low-speed asynchronous motor direct-driven submersible cross-flow pump
For asynchronous motor + reducer and low-speed asynchronous motor direct-driven submersible cross-flow pumps, the problems of system vibration and high noise are more prominent, and the structure is more complex. The structure of low-speed asynchronous motors is mainly affected by the large size of the asynchronous motor, and problems such as reduced flow channel cross-sectional area are more prominent.
3 The huge advantages of low-speed and high-torque permanent magnet motors
3.1 Development and application of permanent magnet motors
A permanent magnet motor is a device that uses permanent magnets to establish an excitation magnetic field to achieve electromechanical energy conversion. Since the advent of high-efficiency NdFeB permanent magnet materials with higher magnetic properties and relatively lower prices in 1983, the focus of research and development at home and abroad has shifted to industrial and civilian permanent magnet motors. In the past ten years, it has had many successful applications in various industries. The efficiency of a high-efficiency NdFeB permanent magnet synchronous motor at a rated load is 2%~8% higher than that of an induction asynchronous motor of the same specification, and it can maintain high efficiency and high efficiency within the rated load range of 25%~120%. The large power factor makes the energy-saving effect more significant during light load operation.
3.2 Comparison of the stator and rotor structures of low-speed permanent magnet motors and low-speed asynchronous motors
To further analyze the characteristics of low-speed and high-torque permanent magnet motors, the following is an analysis of the advantages of permanent magnet motors based on the differences in the specific structures of the stator and rotor of 20-pole permanent magnet motors and 20-pole asynchronous motors. Figure 4 shows the stator and rotor of the permanent magnet motor, and Figure 5 shows the stator and rotor of the asynchronous motor.
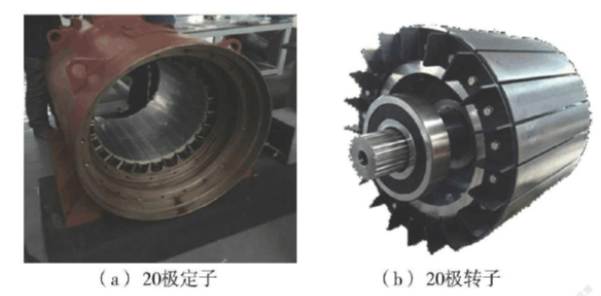
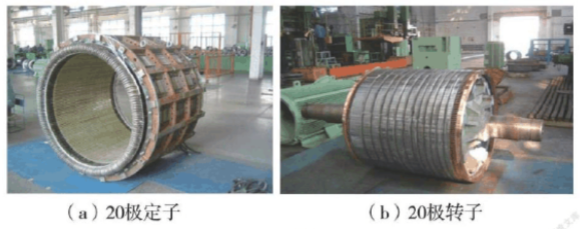
The stator of an asynchronous motor generally has more than 120 coils, and the rotor copper bar generally has more than 100 copper bars. Compared with permanent magnet motors, the stator and rotor processes of asynchronous motors are much more complex, making it difficult for general motor manufacturers to produce them. Especially when the asynchronous motor rotor rotates, the rotor copper bar has low voltage and large current, the rotor also has eddy current and generates a large amount of heat, which brings about thorny heat dissipation problems (generally adopt radial, axial export outside the body and other comprehensive heat dissipation Measures), the rotor volume has to be increased. The permanent magnet motor rotor does not need to dissipate heat, which greatly simplifies the process and structure, and improves safety and reliability.
3.3 Advantages of low-speed permanent magnet motors used in low-speed pumps
Low-speed permanent magnet motors are used in low-speed pumps and have the following advantages:
① Small size, small mass, easy to install, low requirements for basic and other supporting facilities. For example, the mass of a 20-pole 300r/min low-speed permanent magnet motor is only equivalent to 1/2 to 1/3 of an asynchronous motor with the same speed;
②Energy-saving and efficient, the general efficiency of permanent magnet motors is above 96% and the power factor is above 0.97, while the efficiency of asynchronous motors is below 92% and the power factor is around 0.66;
③ Low vibration and noise, low lift and large flow low-speed pump uses a permanent magnet motor drive system. There is no high-speed running part. The motor itself has low noise and vibration. At the same time, the reducer and other transmission devices are eliminated. The reducer and other transmission devices are eliminated. Reduce vibration and noise, making the entire transmission system less vibrating and noisier;
④ Due to the simple structure of the permanent magnet motor, there is no heat dissipation problem in the rotor, so the operation is safer and more reliable, and the maintenance workload is small;
⑤ Easy to intelligently control, using a special frequency converter, convenient speed control, complete fault protection functions, large starting torque, wide speed regulation range, and safe and stable system operation;
⑥Since the rotor has no induced current, the rotor does not generate heat, has low-temperature rise, and is easy to dissipate heat;
⑦ Since the reactive current is very small, the total current of the motor is more than 1/3 less than that of the asynchronous motor, which can reduce the capacity requirements for the upstream power transmission and distribution (including transformers, switches, cables, etc.) and reduce the investment in the power transmission and distribution system.