1. About “Three-phase”
In daily life we encounter most three-phase motors, in household appliances, there are also single-phase motors and two-phase motors with phase numbers 1 and 2. So how exactly is this phase number defined?
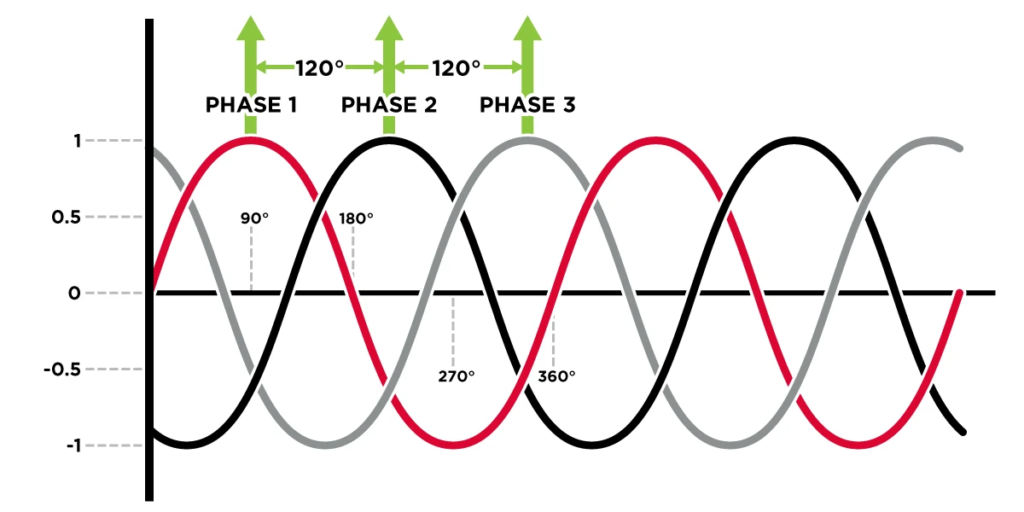
Single-phase: As for the single-phase motor with only 1 straight line, add a capacitor to start, use the shaded-pole method, or start to dial in one direction by hand to run.
Two-phase: One phase can be powered by a single-phase AC power supply, and the other phase can be phase shifted by a capacitor.
This is the two-phase motor that we commonly see on household appliances that run with a capacitor.
Three-phase: Why do we use three-phase motors? There are some reasons:
(1) To make the waveform of the motor’s output more straight after rectification, saving money by eliminating the capacitor for flat waves.
(2) To use three phases to split the phase, making the branches increase and reducing the current in each way to make the power capacity of a single branch smaller.
(3) Using a three-phase motor to increase the reliability of the motor. If one or more phases of the three-phase motor are broken, the other phases can still form a rotating magnetic field and continue to work according to a certain percentage of the original maximum output, which is used in some important equipment.
2. About “synchronous”
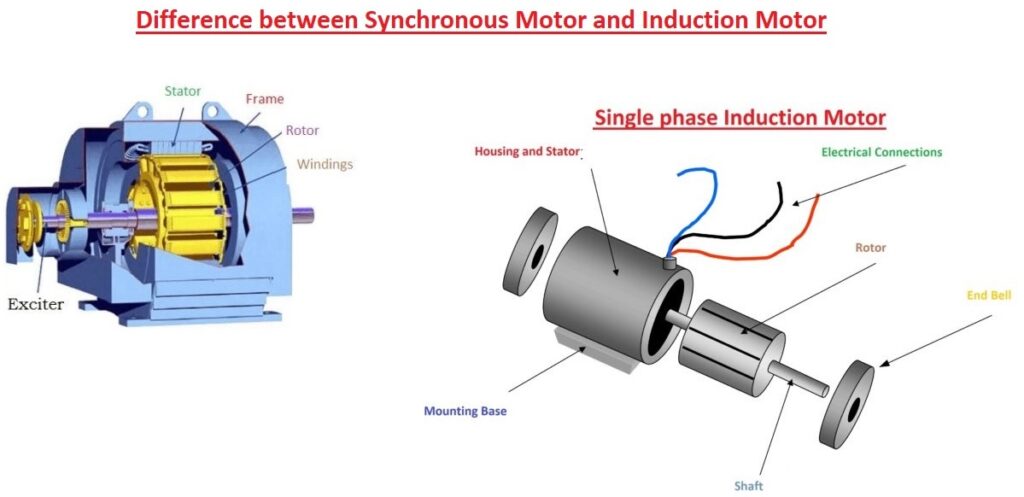
(1) the principle is different
The working principle of the asynchronous motor (induction motor) is to generate induction current in the rotor through the rotating magnetic field of the stator to produce electromagnetic torque, and the rotor does not directly generate the magnetic field.
Therefore, the rotor speed must be less than the synchronous speed (without this difference, i.e., the rate of rotation, there is no rotor induction current), and is therefore called an asynchronous motor.
While the synchronous motor rotor itself produces a fixed direction of the magnetic field (generated by permanent magnets or DC current), the stator rotating magnetic field “drags” the rotor magnetic field (rotor) rotation, so the rotor speed must be equal to the synchronous speed, also called synchronous motor.
(2) the structure is different
The stator winding of the synchronous motor and the asynchronous motor are the same, the main difference is the structure of the rotor.
The synchronous motor has DC excitation winding on the rotor, so it needs an external excitation power supply, and the current is introduced through the slip ring.
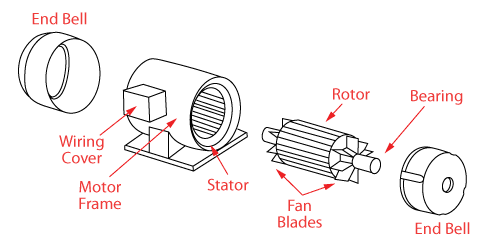
In contrast, the rotor of an asynchronous motor is a short-circuited winding that relies on electromagnetic induction to generate current.
Asynchronous motors are simple, low-cost, and easy to install, use and maintain, so they are widely used.
Disadvantages of low efficiency, low power factor is not conducive to the grid, and synchronous motor efficiency is capacitive load, which can improve the power factor of the grid, mostly used in industrial and mining large equipment.
(3) the advantages of synchronous motors
1. there is no magnetic winding on the rotor, no rotor copper consumption, and high operating efficiency;
2. the rotor rotational inertia is small, and dynamic operation performance is good;
3. low efficiency when the larger power and torque output.
(4) the disadvantages of synchronous motors
High cost, low reliability, complex processing technology, and poor mechanical strength.
(5) the advantages of asynchronous motors
1. no permanent magnet high-temperature demagnetization problem, can be peak power, rated power, peak power working time extended.
2. motor characteristics are affected by the environment is small;
3. itself has a high starting torque, high-speed torque adjustment;
(6) the disadvantages of asynchronous motors
Existence of the copper consumption of the rotor, the energy conversion rate is lower than the permanent magnet synchronous motor.
In contrast, the synchronous motor performance is more excellent.
What we offer is not just the motor, but the drive solution. Contact ENNENG to get Effective Energy-saving Solutions.
3. About “AC”
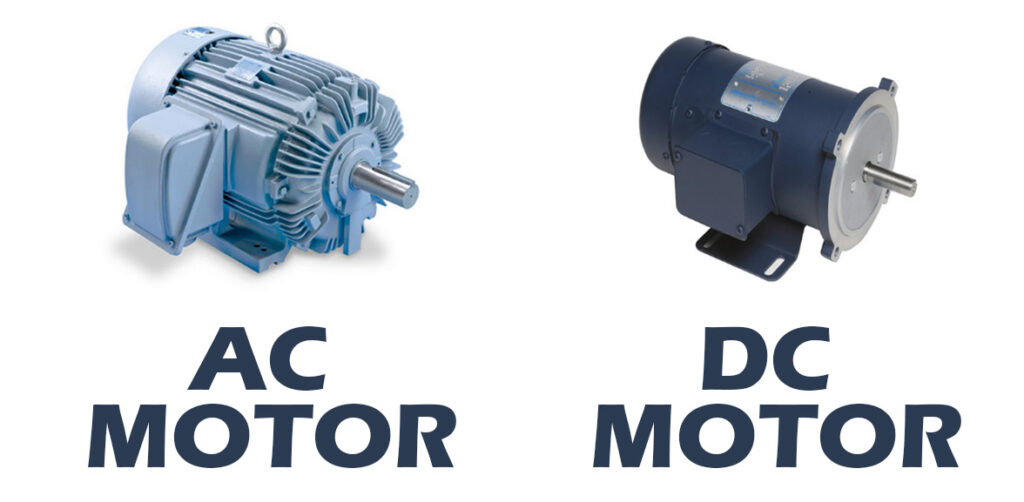
- First of all, the external power supply of the two is different, DC motors use DC as the power supply; while AC motors use AC as the power supply.
- In terms of structure, the principle of the former is relatively simple, but the structure is complex and not easy to maintain; while the principle of the latter is complex but the structure is relatively simple, and it is easier to maintain than the DC motor.
- DC motor is the magnetic field that does not move, the conductor in the magnetic field movement; AC motor is the magnetic field rotational movement, while the conductor does not move.
- In terms of speed regulation, the DC motor can achieve smooth and economic speed regulation, without the cooperation of other equipment, as long as the input or excitation voltage and current can be changed to achieve speed regulation; while the AC motor itself can not complete the speed regulation, need to use frequency conversion equipment to achieve speed changes.
- The motor structure is different, the DC motor through the DC electricity, will not directly produce a rotating magnetic field, it relies on the rotor rotating commutator at any time to change the direction of the current into the rotor so that the polarity of the magnetic field between the rotor stator has been opposite so that the rotor can rotate; and AC motor because of the use of alternating current, as long as the stator coil according to the phase layout, will naturally produce a rotating magnetic field.
4. PMAC vs BLDC
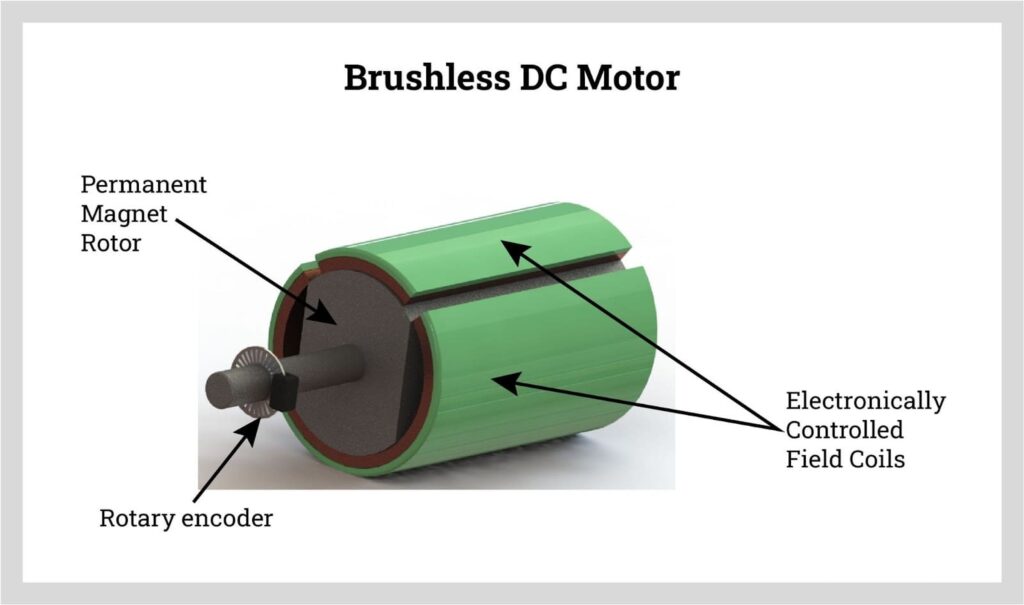
- Brushless DC motors usually use tile-type magnets for the rotor poles, and the magnetic circuit is designed to obtain a trapezoidal wave of air-gap magnetic density, and the stator winding mostly uses a concentrated whole-pitch winding, so the induced counter-electromotive force is also trapezoidal.
- Brushless DC motor control requires position information feedback, and must have position sensors or use position sensorless estimation technology to form a self-controlled speed control system.
- The current of each phase is also controlled as a square wave as much as possible, and the inverter output voltage is controlled according to the method of PWM for brushless DC motors.
- Generally speaking, AC permanent magnet synchronous motor has a stator three-phase distribution winding and permanent magnet rotor, in the magnetic circuit structure and winding distribution to ensure that the waveform of induction potential is sinusoidal, the applied stator voltage and current should also be sinusoidal waveform, generally rely on AC variable voltage inverter to provide.
- The permanent magnet synchronous motor control system is often a self-control type, also needs position feedback information, and can use vector control (magnetic field directional control) or direct torque control of advanced control methods.
5. Number of poles of the motor
The number of poles of a three-phase asynchronous motor is the number of poles in the stator field. The number of poles of the stator field can be formed by different ways of connecting the stator windings.
The number of poles of the motor is determined by the speed required by the load, and the number of poles of the motor directly affects the speed of the motor.
Each set of coils of a three-phase AC motor produces N and S poles, and the number of poles contained in each phase of each motor is the number of poles. Since the poles appear in pairs, there are 2, 4, 6, and 8 poles in motors.
How to divide the number of motor poles?
Two poles are called high-speed motors, four poles are medium speed, six levels are low speed, and greater than or equal to eight poles are called ultra-low speed.
6. IEC standards of the motor
System efficiency being a key factor, efficiency standards for motors are defined by regional governing bodies such as International Electrotechnical Commission (IEC) in the European Union, and National Electrical Manufacturers Association (NEMA) in the United States (US).
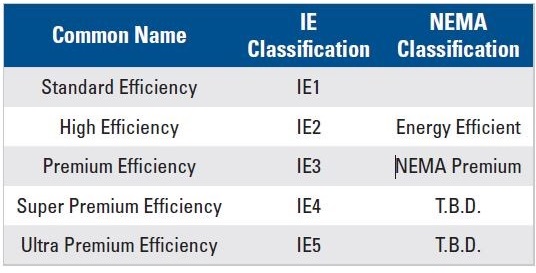
Present IEC motors standards have four levels.
These IEC 60034-30-1 efficiency classes are:
1. IE1 (standard efficiency)
2. IE2 (high efficiency)
3. IE3 (premium efficiency)
4. IE4 (super premium efficiency)
These standards define the efficiency of 50 and 60 Hz motors with single- or three-phase windings built with any type of motor technology (brushless DC or induction, and so on) with the power output higher than 120W.
7. IPM vs SPM
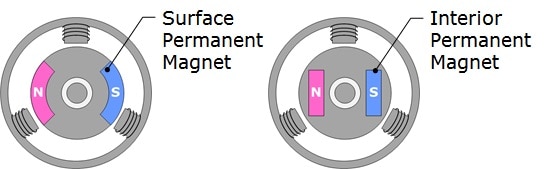
The rotor magnetic circuit structure of the permanent magnet synchronous motor is different, then the operation characteristics and control system of the motor are also different.
According to the position of the permanent magnet on the rotor, the permanent magnet synchronous motor can be mainly divided into the surface type and Interior type.
SPM motors have magnets affixed to the exterior of the rotor surface, their mechanical strength is so weaker than the IPM one. The weakened mechanical strength limits the motor’s maximum safe mechanical speed.
In addition, these motors exhibit very limited magnetic saliency (Ld ≈ Lq). Inductance values measured at the rotor terminals are consistent regardless of the rotor position.
Because of the near unity saliency ratio, SPM motor designs rely significantly, if not completely, on the magnetic torque component to produce torque.
IPM motors have a permanent magnet embedded into the rotor itself. Unlike their SPM counterparts, the location of the permanent magnets makes IPM motors very mechanically sound, and suitable for operating at very high speeds.
These motors also are defined by their relatively high magnetic saliency ratio (Lq > Ld). Due to their magnetic saliency, an IPM motor has the ability to generate torque by taking advantage of both the magnetic and reluctance torque components of the motor.