When users purchase screw air compressors, the design standard is the gas volume and pressure required for full-load production. Therefore, when selecting a model, they can only determine the motor capacity of the screw air compressor according to the maximum demand, resulting in a generally large margin in the air compressor system. Traditional air compressors all use star-delta step-down starting. When starting at power frequency, the current can reach 2 to 3 times the rated current. The current impact is large, directly affecting the power grid’s stability. In addition, most air compressors are operated continuously. Since the motor of a general air compressor itself cannot reduce the speed according to the change in pressure, the motor output power matches the actual pressure demand on site, it still has to run at no load when the gas consumption is small, resulting in a huge waste of electricity.
01 Centralized control method
A centralized control method is adopted for multiple air compressors. The number of air compressors in operation is automatically controlled according to the gas consumption. Before the transformation, the number of air compressors turned on is fixed.
(1) When the gas consumption is reduced to a certain amount, the air compressor reduces the gas production by reducing the loading time.
(2) If the gas consumption is further reduced, the air compressor with good performance will automatically shut down. In the case of (1), the air compressor consumes electricity even when it is unloaded. After the transformation, the corresponding number of air compressors can be shut down, and the number of running air compressors is reduced, undoubtedly saving electricity.
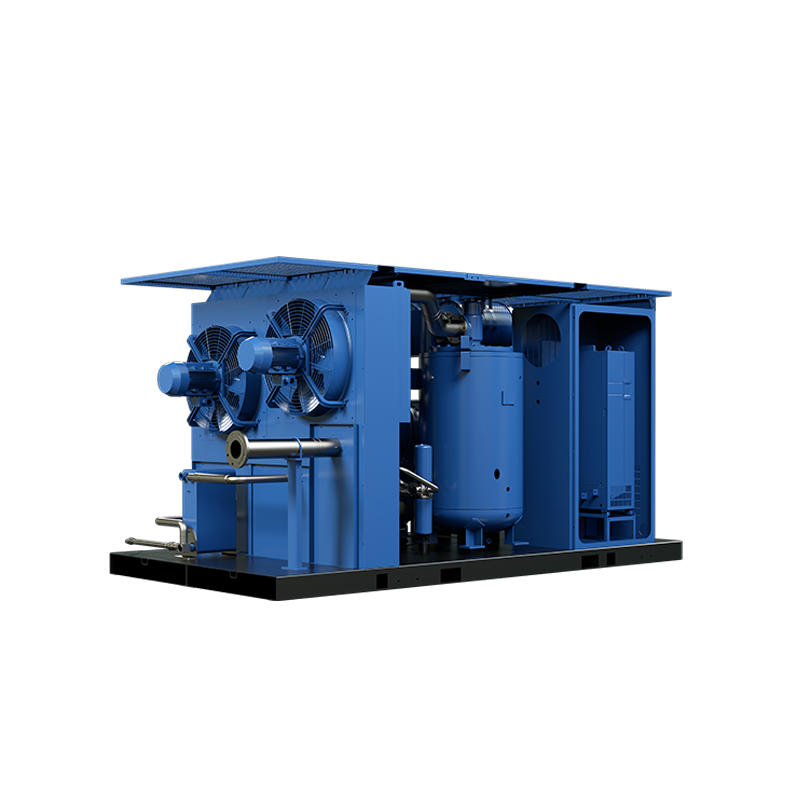
02 Variable frequency speed regulation method
The variable frequency speed regulation method is used to reduce the shaft power output of the air compressor motor. Before the transformation, the air compressor will automatically unload when the pressure reaches the set pressure; after the transformation, the air compressor does not unload but reduces the air production by reducing the speed to maintain the minimum pressure required by the gas network. There are two ways to save energy:
(1) Reduce the power consumption caused by the sudden change from the unloading state to the loading state of the compressor.
(2) The operating frequency of the motor is reduced to below the working frequency so that the output power of the motor shaft is reduced.
03 Soft start energy saving
04 Power factor compensation energy saving
Reactive power not only increases line loss and equipment heating but more importantly, the reduction of power factor leads to a reduction in the active power of the power grid. A large amount of reactive power is consumed in the line, and the equipment is inefficient and wasteful. After using the frequency conversion speed regulation device, due to the effect of the internal filter capacitor of the inverter, the reactive loss is reduced and the active power of the power grid is increased.